Common Challenges Faced In Aluminum Alloy Wire Drawing Machine Operations
Aluminium wire drawing is a process used to reduce the diameter of aluminum wire by pulling it through a series of dies. This process is essential in the production of various aluminium products, such as electrical wiring, cables, and conductors.One common challenge faced in aluminum wire drawing operations is die wear. As the wire is pulled through the dies, friction and pressure cause the dies to wear down over time.To mitigate this challenge, regular maintenance and inspection of the dies are essential. Additionally, using high-quality dies made from materials with high wear resistance can help prolong their lifespan.
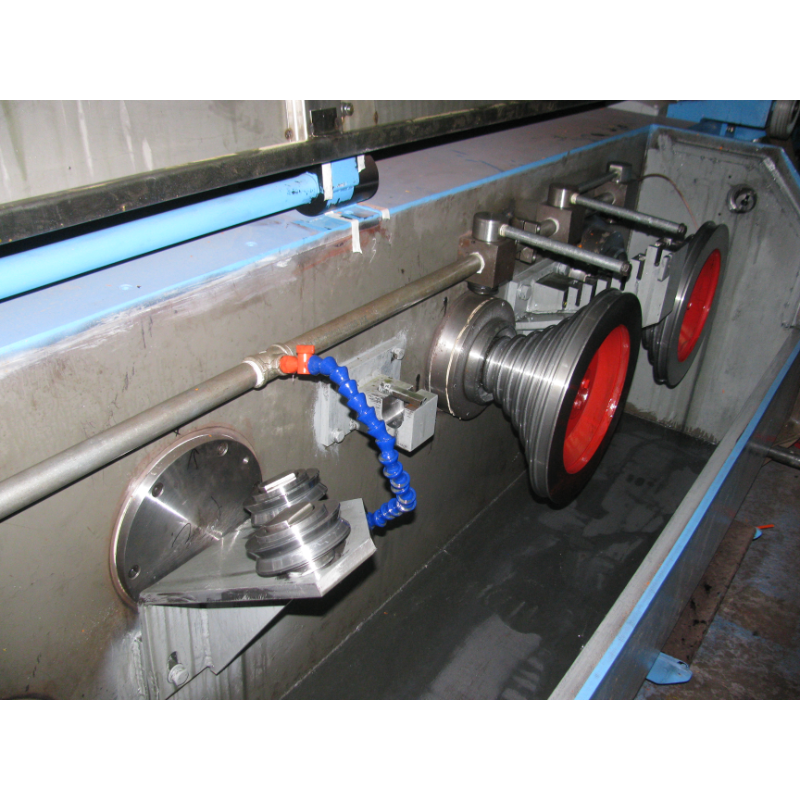
Another challenge in Aluminum Wire Breakdown Machine is surface quality. The surface of the wire can be affected by various factors, such as die wear, lubrication, and drawing speed. Poor surface quality can lead to issues like surface defects, roughness, and reduced conductivity. To improve surface quality, it is important to use proper lubrication during the drawing process and ensure that the dies are in good condition. Adjusting the drawing speed and tension can also help achieve a smoother surface finish.
Dimensional accuracy is another critical aspect of aluminium wire drawing. Variations in wire diameter can impact the performance and functionality of the final product. Factors like die wear, material properties, and drawing parameters can affect dimensional accuracy. To address this challenge, it is important to monitor and control the drawing parameters, such as die size, reduction ratio, and drawing speed. Regular calibration of equipment and dies can also help maintain dimensional accuracy throughout the drawing process.
One of the most significant challenges in aluminium wire drawing is material properties. Aluminum is a soft and ductile metal, which can make it prone to deformation and breakage during the drawing process. Controlling the material properties, such as alloy composition, grain size, and microstructure, is crucial to achieving consistent and high-quality wire. Proper heat treatment and annealing processes can help improve the mechanical properties of the aluminium wire, making it more suitable for drawing operations.
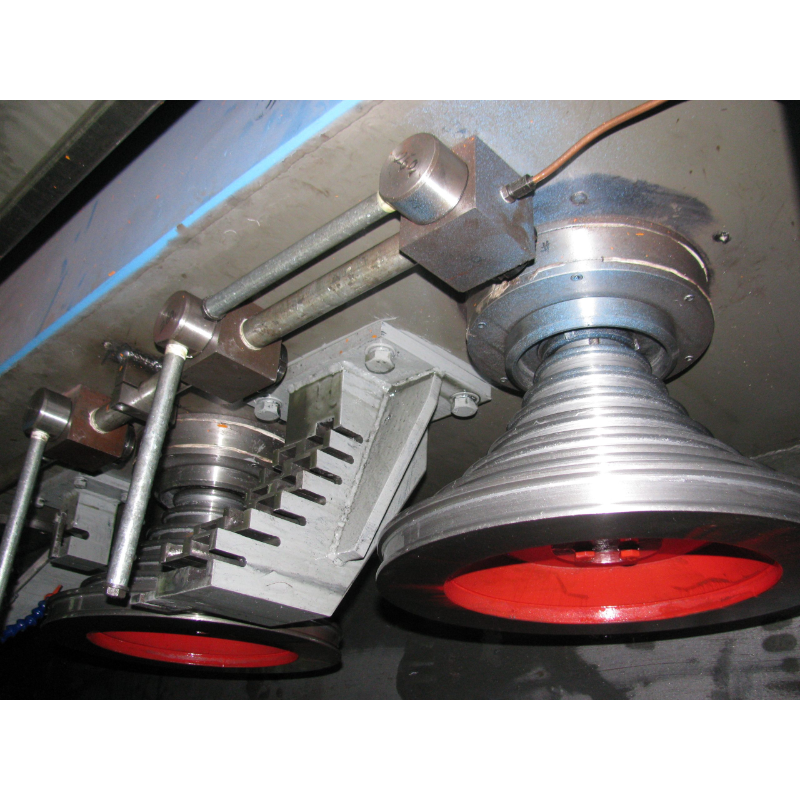
In conclusion, aluminum wire drawing operations face several common challenges that can impact the quality and efficiency of the process.By addressing these challenges through proper maintenance, control of drawing parameters, and material optimization, manufacturers can produce high-quality aluminium wire for various applications. Continuous improvement and innovation in the wire drawing process are essential to overcome these challenges and meet the demands of the industry.