Tips for Optimizing Efficiency in Enameling Machine
Enameling machines are essential for manufacturing heat exchangers used in various industries such as HVAC, automotive, and aerospace. These production lines involve multiple processes such as cleaning, coating, drying, and curing to ensure the quality and durability of the final product. To optimize efficiency in a heat exchange Enameling Wire Production Line, it is crucial to implement certain tips and strategies that can streamline the production process and improve overall productivity.
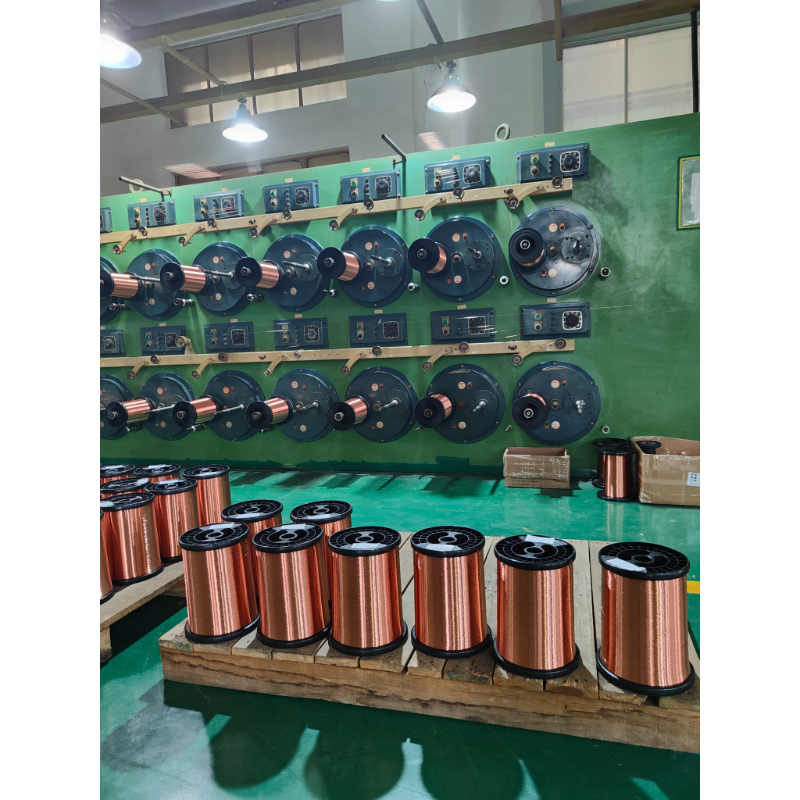
One key tip for optimizing efficiency in a heat exchange enameling production line is to ensure proper maintenance of equipment and machinery. Regular maintenance and servicing of equipment such as ovens, conveyors, and coating machines can help prevent breakdowns and downtime, which can significantly impact production output. It is important to schedule routine maintenance checks and inspections to identify any potential issues and address them promptly to avoid disruptions in the production process.
Another tip for optimizing efficiency is to implement automation and robotics in the production line. Automation can help streamline repetitive tasks and improve accuracy and consistency in the production process. By automating certain processes such as coating application and curing, manufacturers can reduce labor costs, minimize errors, and increase production speed. Investing in automation technology can also help improve overall product quality and consistency, leading to higher customer satisfaction.
Furthermore, optimizing the layout and design of the Wire Enameling production line can also help improve efficiency. By organizing equipment and workstations in a logical and efficient manner, manufacturers can reduce unnecessary movement and transportation of materials, which can save time and improve workflow. It is important to analyze the flow of materials and personnel in the production line and make adjustments to optimize efficiency and minimize bottlenecks.
In addition, implementing lean manufacturing principles can help optimize efficiency in a Enameling Machine for copper wire. Lean manufacturing focuses on eliminating waste, improving processes, and maximizing value for the customer. By identifying and eliminating non-value-added activities, manufacturers can streamline the production process, reduce lead times, and increase productivity. Implementing lean tools such as 5S, kanban, and value stream mapping can help identify areas for improvement and drive continuous improvement in the production line.
Moreover, training and development of personnel are essential for optimizing efficiency in a heat exchange enameling production line. Providing employees with proper training on equipment operation, safety procedures, and quality standards can help improve productivity and reduce errors. It is important to invest in ongoing training and development programs to ensure that employees have the necessary skills and knowledge to perform their jobs effectively.
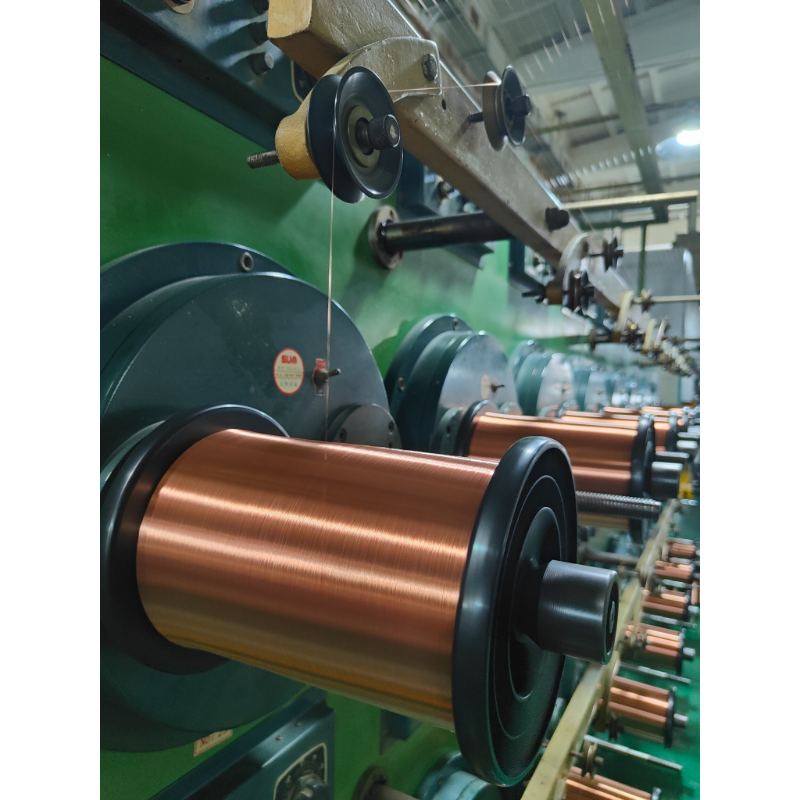
In conclusion, optimizing efficiency in a heat exchange enameling production line requires a combination of proper maintenance, automation, layout design, lean manufacturing principles, and employee training. By implementing these tips and strategies, manufacturers can streamline the production process, improve productivity, and enhance overall efficiency in the production line. Ultimately, optimizing efficiency can help manufacturers meet customer demands, reduce costs, and stay competitive in the market.